Taisei's Carbon_Recycled Concrete (T-eConcrete®/Carbon-Recycling)
Enhancing the lineup of T-eConcrete®, an environmentally friendly concrete, as well as effectively utilizing resources and realizing decarbonization
In order to achieve carbon neutrality by 2050, efforts are underway to "carbon recycle" to curb CO2 emissions by recovering and effectively utilizing CO2 as a resource.
Taisei Corporation has developed various types of environmentally friendly concrete, its T-eConcrete®, and is committed to the effective use of resources and decarbonization.
Going forward, we aim to be a front-runner in the environmental sector and will accelerate our efforts to become carbon neutral by accumulating experience in applications for concrete that "creates the future."
Characteristics and Variations of T-eConcrete®
T-eConcrete® limits the amount of cement used, maintains the same strength and workability as ordinary concrete and is also able to reduce CO2 emissions.
There are four types, depending on the mixture conditions for such items as industrial by-products added in place of cement: Japanese Building Standards Law compliant type, Fly ash utilization type, Zero-Cement type, and Carbon-Recycling. Depending on the intended use, concrete of appropriate specifications can be developed.
- Building Standards Law compliant type:
Reducing cement, the binder replaces that with ground granulated blast furnace slag (GGBFS) (discharged as an industrial by-product at steelworks).
It is suitable for building construction that complies with Japan’s Building Standards Law. - Fly ash utilization type:
Reducing cement, the binder replaces that with ground granulated blast furnace slag (GGBFS) and fly ash (a type of coal ash).
Coal ash, an industrial by-product of coal-fired power plants, can be effectively utilized. - Zero-Cement type:
Without using any Portland cement, this type is made using ground granulated blast furnace slag (GGBFS) and special additives as activators or stimulators.
It enables a maximum amount (up to 80%) of CO2 reduction. - Carbon-Recycling:
Without using any Portland cement, this type is made using carbon-recycled materials such as calcium carbonate, and ground granulated blast furnace slag (GGBFS) and special additives as activators or stimulators.
By absorbing CO2 internally within the concrete, there are negative CO2 emissions (balance of absorption and emission).
T-eConcrete® variations and their CO2 emissions
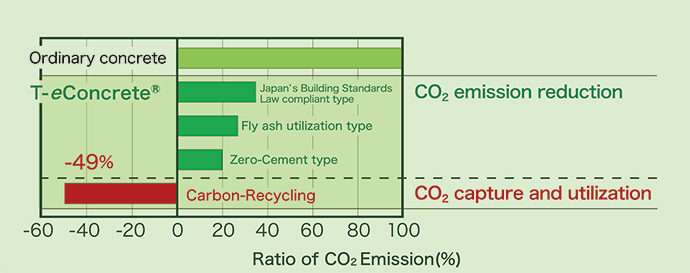
From among these, we will introduce in detail the characteristics of T-eConcrete®/Carbon-Recycling,which uses CO2 as a resource.
What Is T-eConcrete®/Carbon-Recycling (Carbon _Recycled Concrete)?
Carbon-recycled concrete is manufactured using carbon-recycled materials such as calcium carbonate, which is produced by reacting calcium with CO2 captured from exhaust gases, and ground granulated blast furnace slag (GGBFS), an industrial by-product of steel manufacturing. CO2 can be absorbed inside the concrete by converting CO2 into calcium carbonate and mixing it into the concrete.
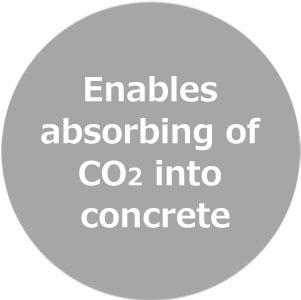
Absorbing 98kg to 171kg of CO2 per 1m3 of concrete
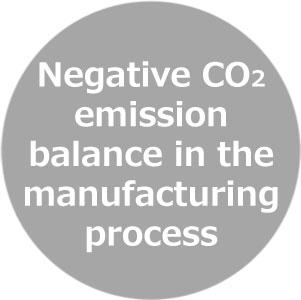
Negative balance of -116kg to -45kg per 1m3 of concrete
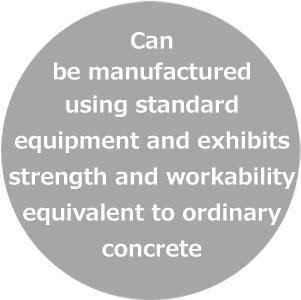
Strength characteristics (compressive strength: 20–45N/mm2) and flowability (slump: 12–21cm, slump flow: 45–60cm), which is an indicator of workability, are equivalent to those of ordinary concrete, and can be manufactured at ordinary ready-mixed concrete plants without special equipment.
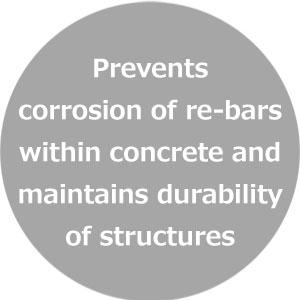
Able to maintain strong alkaline inside concrete, prevents corrosion of re-bars and maintains durability of reinforced concrete structures
Example of balance between CO2 absorption and emissions
【Cast-in-place paving in front of Human Space Lab in Taisei Advanced Center of Technology】

"Carbon_Recycled Concrete" has been developed with calcium carbonate manufactured by absorbing CO2 from exhaust gas, and is produced by mixing calcium carbonate, ground granulated blast furnace slag (GGBFS) and special additives as activators or stimulators. Per 1m3 of Carbon_Recycle Concrete, the "amount of CO2 absorbed" by calcium carbonate is 171kg/m3, whereas the "amount of CO2 emitted" into the air during manufacturing process of calcium carbonate, GGBFS and others is 55kg/m3, then the balance of CO2 emissions of Carbon_Recycled Concrete is -116kg/m3, achieving "Carbon Negative".
Carbon-recycled concrete cross-sections
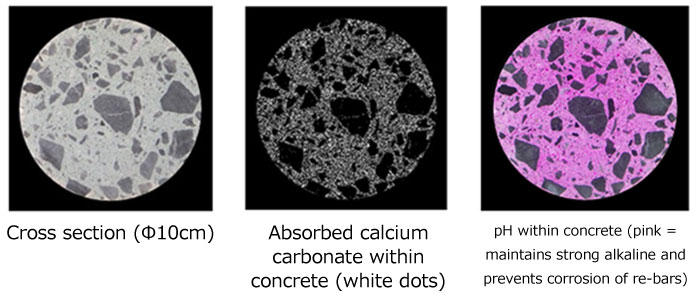
T-eConcrete®/Carbon-Recycling Manufacturing Process and Status
Manufacturing process
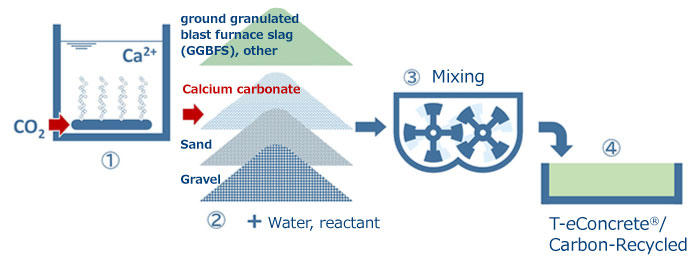
- 1Inject the captured CO2 into an aqueous solution in which calcium is dissolved to produce calcium carbonate absorbed with CO2
- 2Add aggregates such as sand and gravel, together with water and additives, to blast furnace slag and calcium carbonate with absorbed CO2
- 3Mix the added ingredients in a mixer
- 4T-eConcrete®/Carbon-Recycling (carbon-recycled concrete) is completed
Manufacturing status
- *Link to YouTube.
Information on viewing lecture archives
- *Link to YouTube.
Lecturer name | Nikkei SDGs Festival, Green Architecture A Materials Revolution That Is Transforming Society, On-Site Manufacturing of "CO2 Recycle Concrete" |
---|
Application Case Studies / External Awards
Application case study (carbon-recycled concrete)
Interior wall components of experimental facility
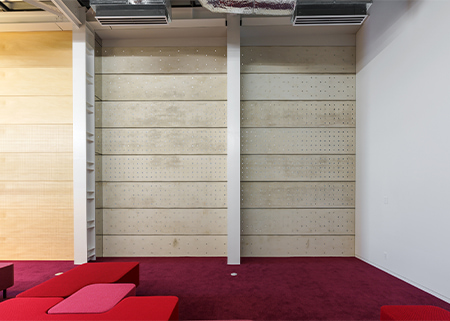
Cast-in-place pavement (red box) and stone-like paving blocks (blue box)
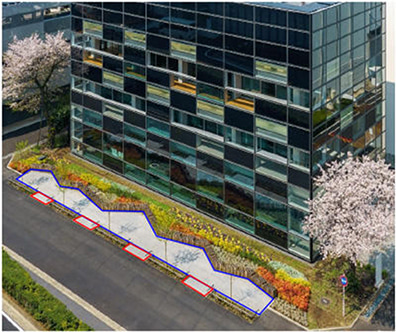
Application case study (Zero-Cement type)
Applied as cast-in-place concrete
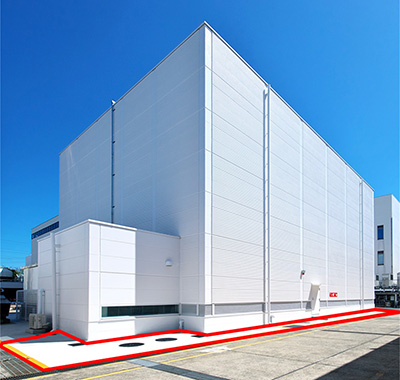
Concrete products manufactured by members of T-eConcrete® Research Group
Civil engineering structures
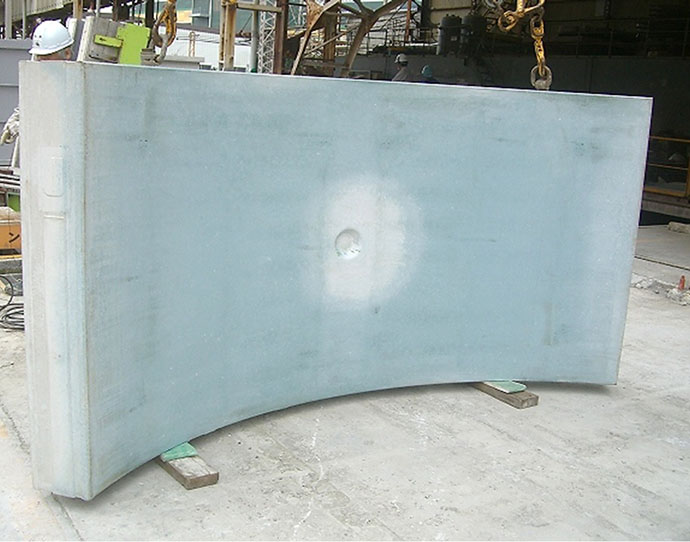
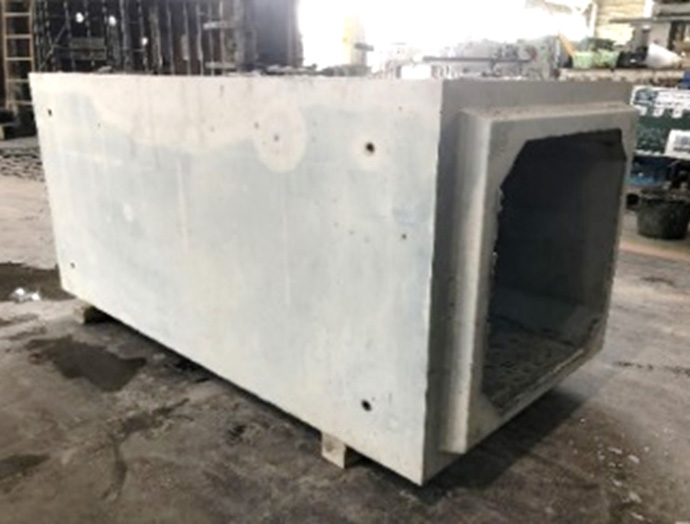
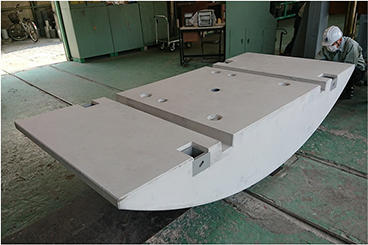
T-razzo®; Stone-like building materials
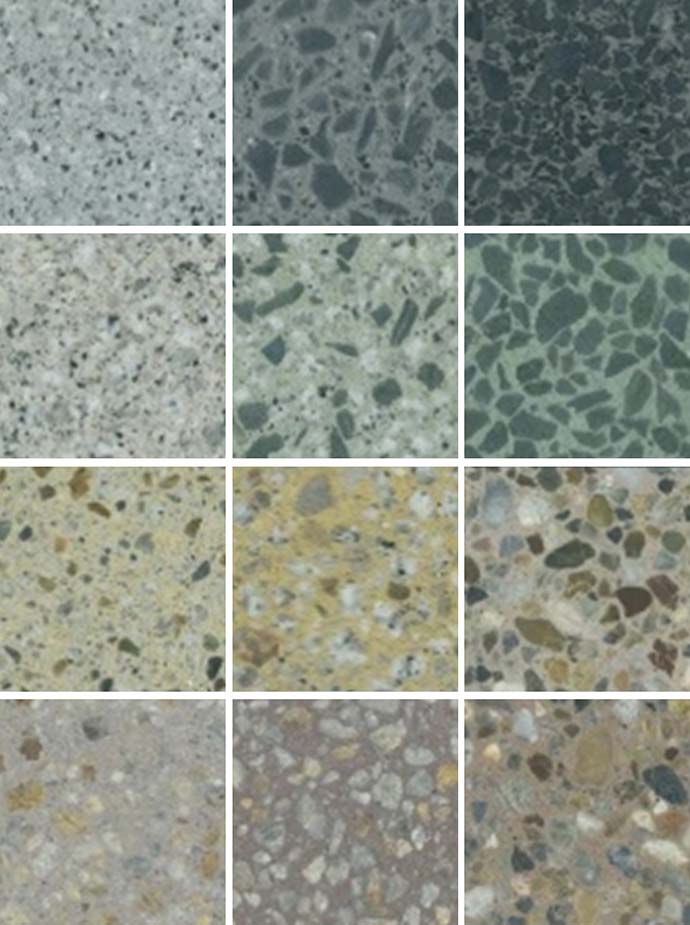
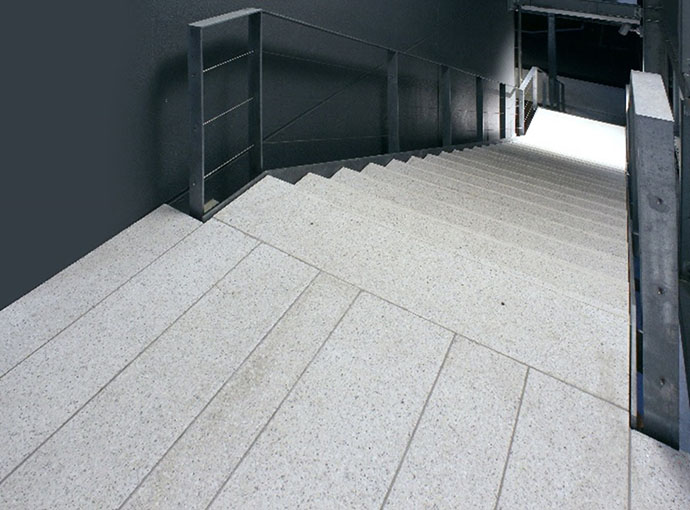

External awards
- Japan Society of Civil Engineers (JSCE)
JSCE 2014 Environmental Award (Group-I) (Presented jointly to Public Works Research Institute)
- Engineering Advancement Association of Japan (ENAA)
13th Engineering Commendation Award of ENAA 2021
Promising cutting-edge technology for commercialization: Project team for the creation of concrete products with environmentally friendly concretes